The Hot-Dip Galvanizing Process
Hot-dip galvanizing (HDG) is a proven method for protecting steel from corrosion. This process involves immersing fabricated steel in a bath of molten zinc to create a durable, long-lasting barrier. The Key Steps of HDG include Surface Preparation, Galvanizing & Inspection.
Surface Preparation
The Steel arrives at our galvanizing facility and is cleaned. This involves degreasing to remove dirt, oil, and organic residues. Pickling, an acidic bath, removes mill scale and iron oxide (rust). Finally, fluxing removes any remaining oxides and preps the surface for a strong zinc bond. Proper preparation is crucial as zinc won’t adhere to unclean steel.
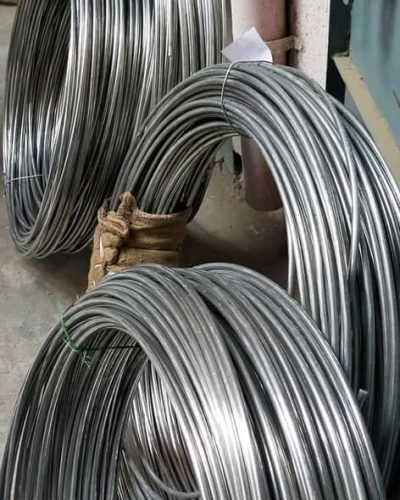
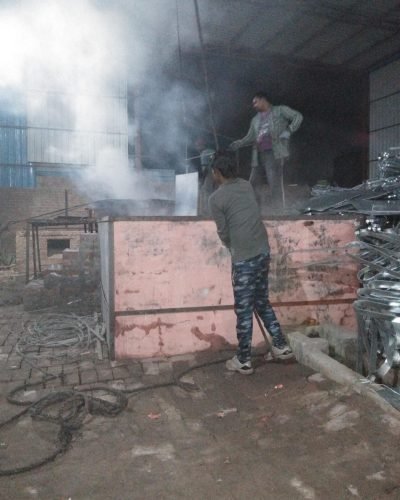
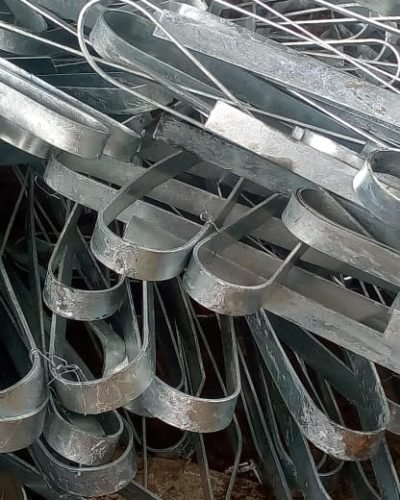

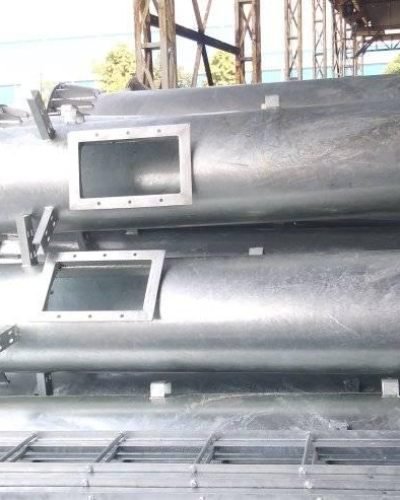
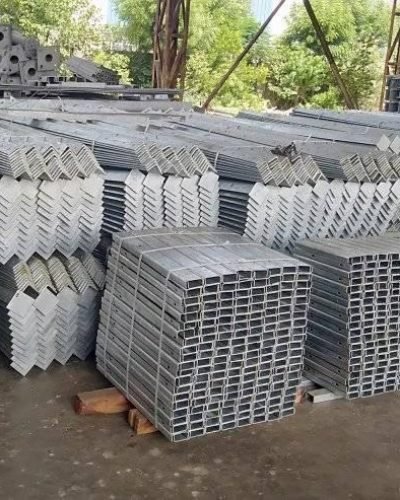
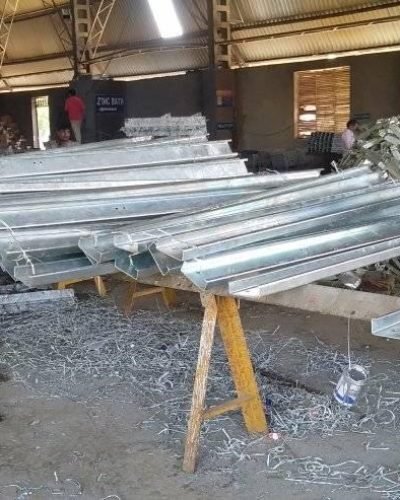
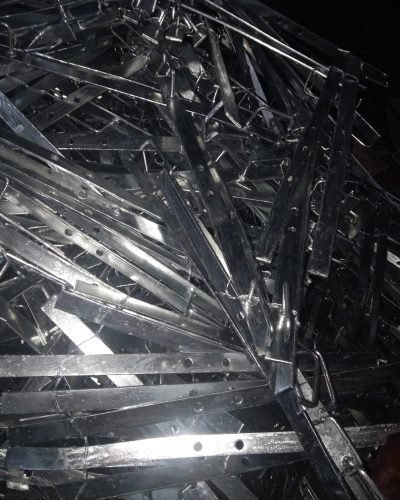
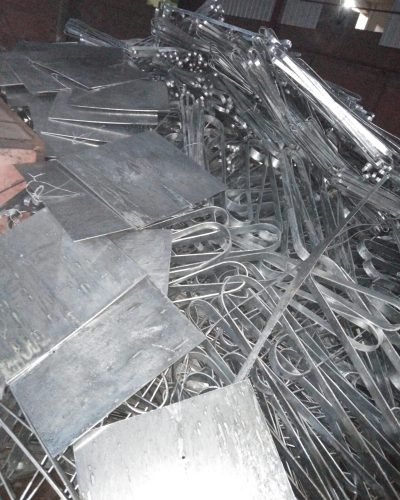
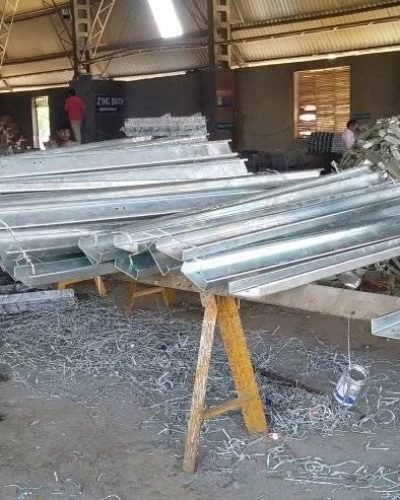
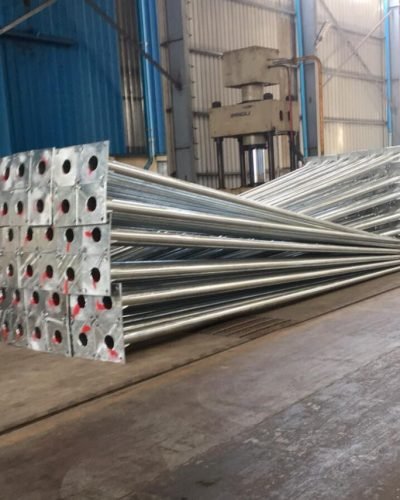
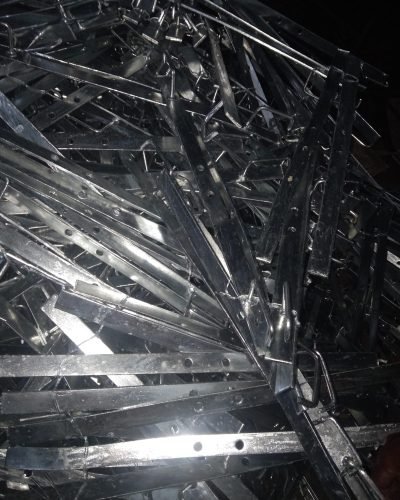
Galvanizing
The cleaned steel is then dipped into a molten zinc bath at around 450°C (842°F). This triggers a metallurgical reaction, forming a zinc-iron alloy layer that bonds firmly to the steel.
Inspection
After galvanizing, the steel undergoes a final inspection to ensure it meets quality and thickness standards.
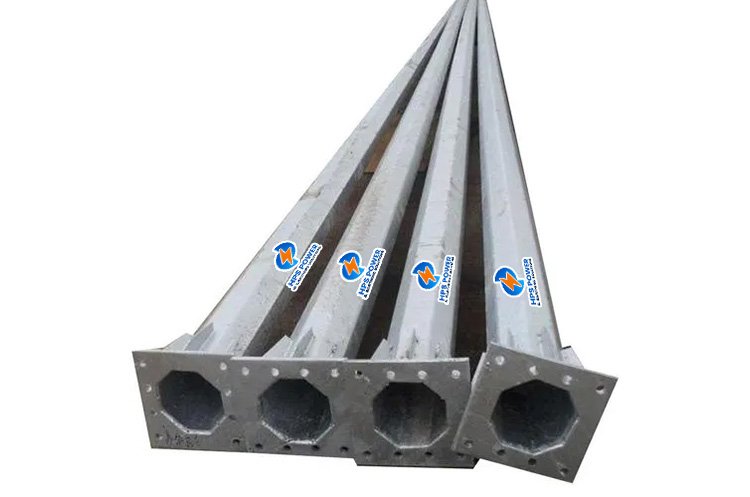
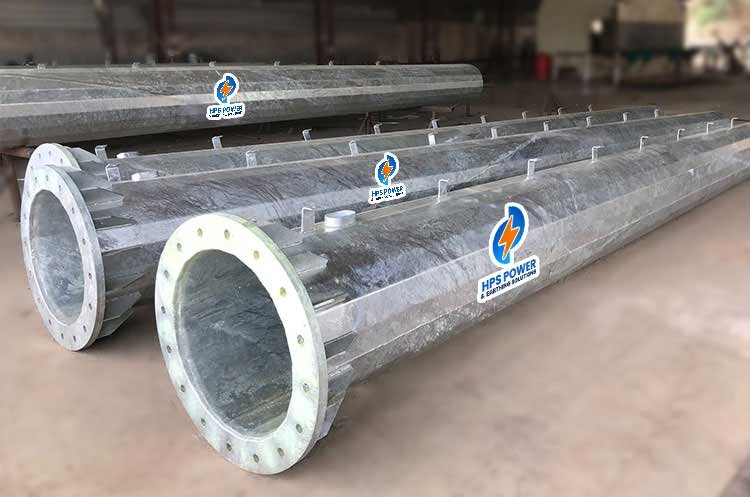
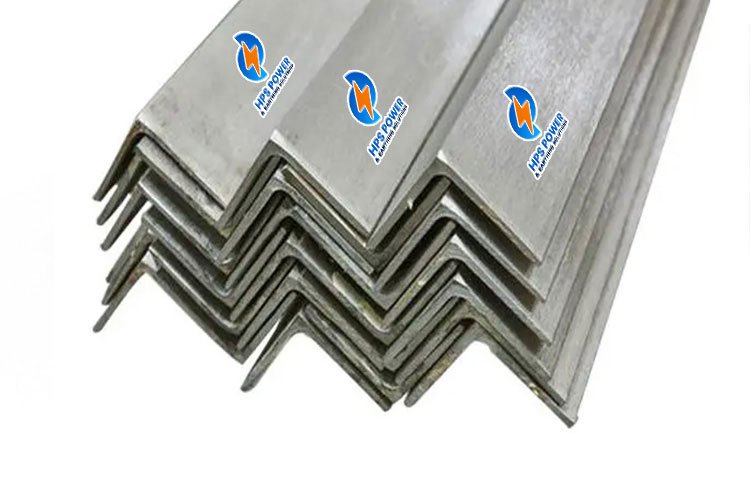
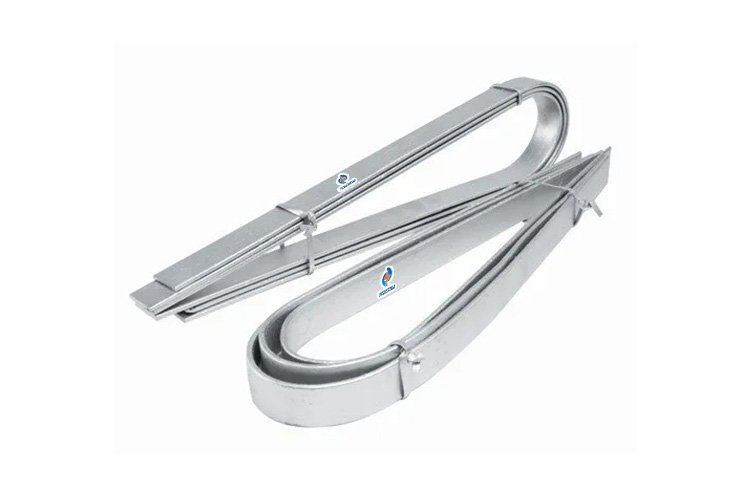
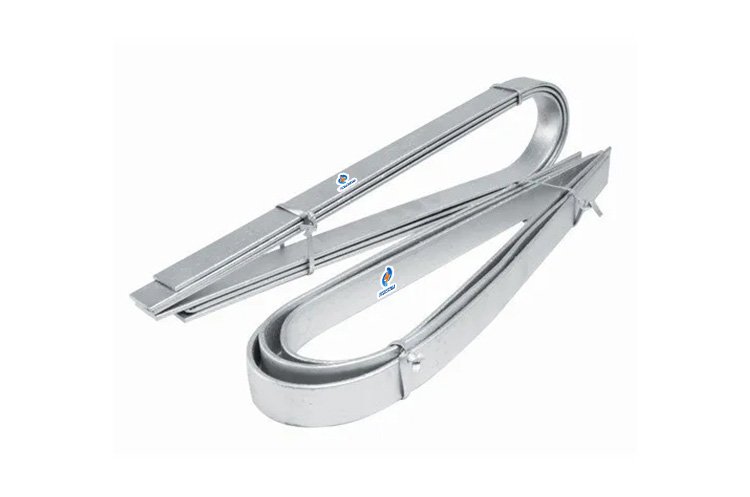
Benefits of HPS Hot-Dip Galvanizing:
- Long-lasting Corrosion Protection
- Low Maintenance
- Versatility